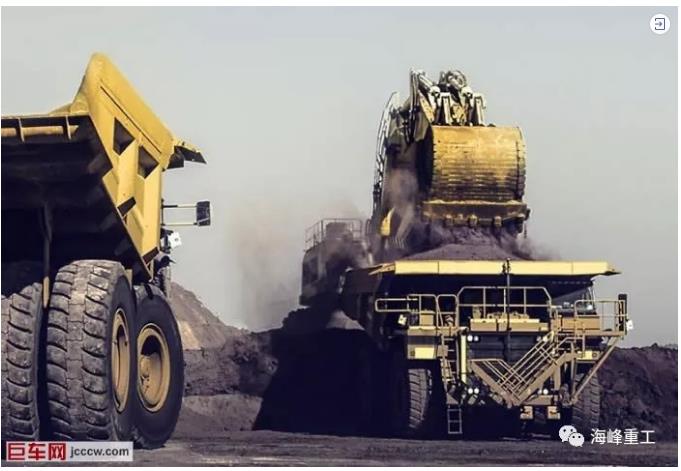
In a report on mining innovation and new technologies, Australian RFC Ambrian talked about automated mining equipment, which it said was "very mature".
The report covers surface mining and underground mining, with special emphasis on surface mining trucks, which are also the key areas of concern for major mining companies. "Although the technology is still developing and has not been used in the industry for a long time, it is very mature," the report said.
AHS (Automated Transportation System)
The report says that the development of AHS has benefited from improvements in GPS for positioning and navigation, the development of sensors and detection technologies, especially radar and lidar, the improvement of computing and vehicle monitoring capabilities, faster and more stable network and Internet connections, and the development of efficient, high-precision algorithms and software.
"AHS first appeared in large-scale mining operations, due to the high proportion of fixed costs in the operation of AHS, resulting in the greatest benefits; first appeared in developed countries lacking skilled workers and high labor costs." The author of the report said.
It is easy to describe the potential advantages of AHS in general, but difficult to find hard data to support it.
"Companies have made proposals to improve the scale, but they lack details, have unclear definitions and have different data from company to company." According to the author.
The report says productivity improvements from Caterpillar, Fortescue, Komatsu and Rio Tinto are 15-20%, 30%, 15% and 15%, respectively.
"These improvements are still significant. Companies will think that every mine is different. Mining companies and original equipment manufacturers that have implemented AHS have the right to protect these proprietary information and maintain their competitive advantage." The author said.
Automation of other surface equipment
The report says the same technology has also been used in other surface mining equipment, including drilling rigs, bulldozers, loaders and auxiliary equipment. "Although some mines use fully automated drills and bulldozers, at least at present most of these equipment are semi-automated," the author said. Full automation of these devices will significantly increase productivity, although the actual effect is not as significant as that of AHS. However, we have not yet seen the downstream benefits quantified after the improvement of drilling and blasting operations.
"The automation of earthwork machinery has increased mining productivity a step further, but due to the variability of loading direction and the risk of collision with trucks, loading equipment is facing more challenges."
Because of the complexity of bucket interaction function, it is very difficult to develop automatic loading function which is superior to or equivalent to the performance of professional drivers, the author said. "As a result, fully automated loading has not yet been commercialized. Some observers believe that it will take five years for fully automated surface loading to be used, while others feel that full automation is impossible to achieve."